Torque Bucket
Bespoke subsea polymer solutions, designed to enhance performance and impact real change.
What is a Torque Bucket?
The ROV Torque Bucket is a robust, bespoke solution deployed in subsea operations to facilitate the controlled application of torque by a Remotely Operated Vehicle (ROV). Designed to industry-standard specifications (typically ISO 13628-8 / API 17H), the torque bucket ensures safe, repeatable engagement with various subsea tools and valves in subsea operations. Engineered for durability in harsh marine environments, it plays a critical role in enabling efficient maintenance, installation, and intervention tasks across oil and gas, renewable, and offshore infrastructure sectors.
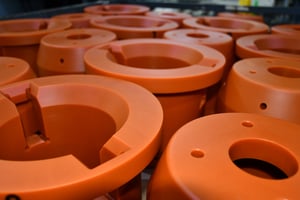
Why Choose Polymer ROV Torque Buckets?
Polymer ROV torque buckets offer a range of advantages over traditional metallic alternatives, making them an ideal choice for demanding subsea applications:
Application uses in Industry
Examples of Wear Pads in use:
- Support allows thermal expansion and contraction while protecting painted surfaces.
- Crane booms sliding pads reducing wear on the boom structure.
- Bridge bearings accommodating movement and reducing wear.
- Conveyor systems that guide and support moving parts with minimal wear.
Industry technology that makes use of Wear Pads includes:
- Telehandler
- Mobile Cranes
- Backhoe Loader
- Aerial Work Platforms
- Straddle Carriers
- Forklift
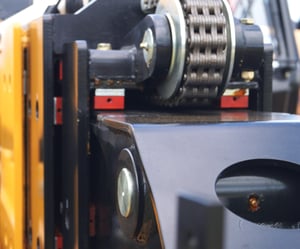
Enhanced Performance Material
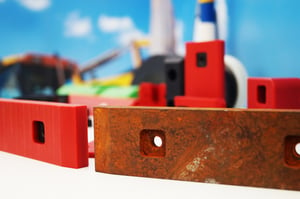
Contact Our Experts
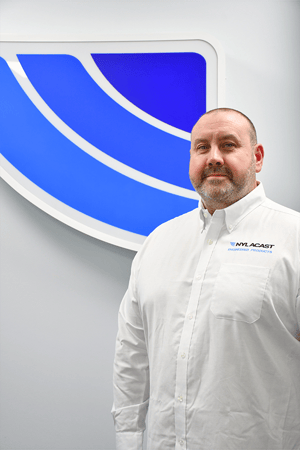
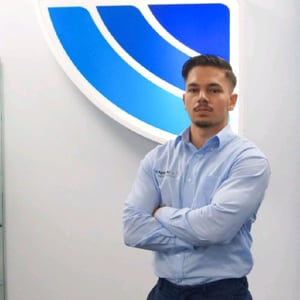
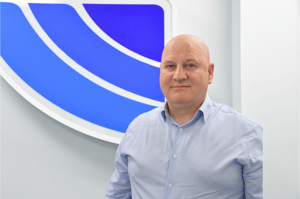
Talk To The Team.
Speak to one of our experts about creating the right solution for your application.We are always happy to help.